Within the framework of the ICEBERG project, VITO and Orbix are working on an innovative way to produce high-grade recycled concrete aggregate assuring the quality of the RCA
Jef Bergmans, Debabrata Gosh (VITO), Peter Van Mierloo (Orbix)
Concrete accounts for about 42% of used construction materials in the EU. The building sector seldomly uses recycled concrete aggregates in high-grade construction products (e.g., concrete walls, brdges, floors, etc.). Currently, the main application for recycled concrete aggregates is as a base material for road construction or as (sub)foundation material. However, the capacity of the road construction sector to absorb recycled aggregates as base materials is limited in mature infrastructure systems. To ensure sufficient recovery options for the concrete fraction of construction and demolition waste (C&DW) in the future, increased high-value applications of C&D waste will need to be developed.
The main barriers to using recycled concrete aggregates (RCAs) are variability of composition of the RCA and higher water absorption compared to natural aggregates. The variability in the composition of the RCA can be tackled by an improved value chain from demolition to new product. By keeping high-quality concrete fractions separate during the selective demolition phase and processing this high-quality concrete into high-grade concrete aggregates for new concrete products, the quality of the RCA is assured.
The increased water absorption of RCA can negatively impact the performance of the concrete mixture. The higher water absorption of RCA will reduce the concrete workability and hence increase the demand for water. However, increasing the water amount in the concrete mixture can also have detrimental effects. The water/cement ratio (w/c ratio) of concrete is an important indicator of its strength and workability, and adding extra water will have a negative effect on this variable.
High water absorption is linked with the presence of old mortar attached to the recycled natural aggregates. A further factor is the air voids and capillary pores at the interfacial transition zone (ITZ). Water absorption values may be less than 1% for natural aggregates, whereas for recycled aggregates they may be over 10%.
Carbonation experiments with 70% CO2 at 40 °C for 24 hours resulted in a 25% reduction in water absorption and a 3-4% increase in particle density
Carbonation of RCA is gaining more attention among researchers because of its positive influence on the physical and mechanical properties of the aggregates and ease of application. Furthermore, mineral carbonation routes are a way to utilise captured CO2 and store it for a long period of time. The calcium- and magnesium-bearing hydration products (portlandite, C–S–H, ettringite and AFm phases) in the hardened cement paste are prone to carbonation and can form stable phases such as calcite and dolomite. In the case of portlandite, carbonation leads to an 11–12% increase in solid volume. This can be correlated with a decrease in the porosity of the old cement matrix, enhanced ITZ and increased mechanical strength.
Experiments with different carbonation conditions (e.g., CO2 concentration, temperature, and carbonation time) were performed on samples of coarse RCA. The carbonated and uncarbonated RCA specimens were then characterized.
Carbonation experiments with 70% CO2 at 40°C for 24 hours resulted in a 25% reduction in water absorption (to water absorption values <5%) and a 3-4% increase in particle density. Per kilogram of concrete aggregates, around 35 g of CO2 is sequestered. Increasing the reactor temperature to 60°C significantly reduced the required carbonation times, with similar water absorption and density results being obtained after a carbonation of 6 hours.
During the rest of the project, the process will be upscaled and the RCA produced will be used for the production of concrete samples.
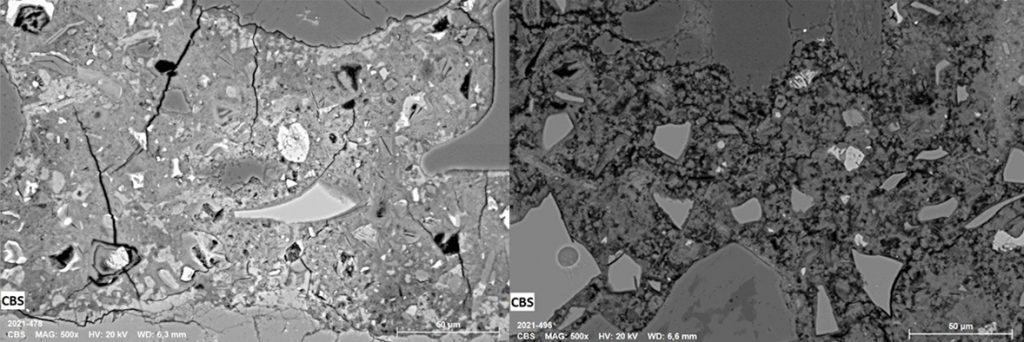