RAMPF Group, Inc. has pioneered the technology to upcycle polyurethane (PU) wastes generated by foam manufacturers and converting them to polyols utilizing multifunctional plants for the upcycling process.
The international RAMPF Group, a partner in the ICEBERG project, has pioneered the recycling of polyurethane wastes – for more than three decades, the company has been developing chemical processes whereby post-consumer PU foam scraps from used mattresses, furniture, car seats, motorcycle seats, insulation materials, as well as fitness and leisure items are upcycled to high-quality polyols.
Using solvolysis (glycolysis, acidolysis, and aminolysis), recycled polyols are manufactured that are at the very least comparable with polyols otherwise obtained from virgin raw materials – both in terms of quality and technical properties. RAMPF recycled polyols are tailored precisely to the customer’s production set-up and can therefore be used directly in the production process for new products.
Furthermore, RAMPF has developed chemical processes that enables PET/PSA, other polyesters (PLA, PC, PHB), and renewable or bio-based raw materials such as vegetable oils to be used as sources of raw materials for the manufacture of bio-based recycled polyols. The company also offers comprehensive advice in polyurethane recycling and developing customized polyols. The formulation of polyurethane systems using a RAMPF recycled polyol and contract manufacturing of molded components are further offerings in the portfolio.
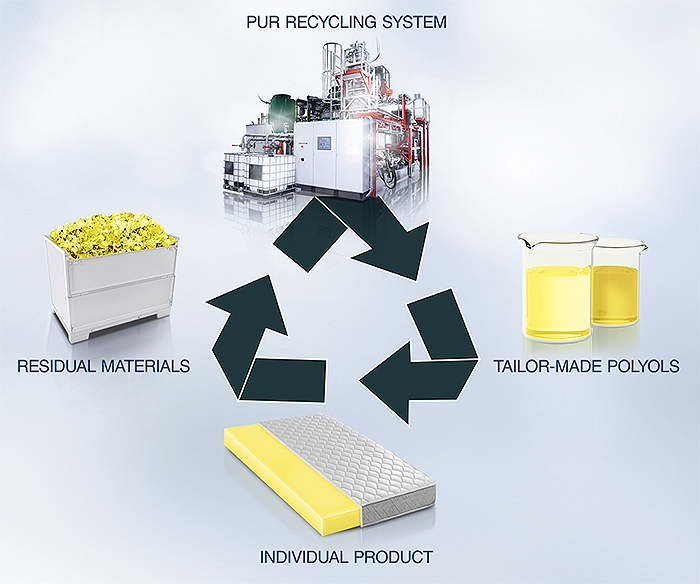
Multifunctional recycling plants
By combining its encompassing experience in chemical solutions in conjunction with the expertise of its partners in industrial plant construction, RAMPF has been very successful on the international markets with a unique product offering – the development of multifunctional recycling plants for their customers. Using their own customized inhouse plants and polyurethane waste materials, PET, phthalic anhydride, and polyisocyanurate, companies can manufacture their own high-quality recycled polyols on site and use these in their production process. In doing so, they cut costs and contribute to the protection of the environment.
For more information: https://labur.eus/Dqyb8