ICEBERG project will develop a new digital tool to support demolition planning and waste assessment. It will be tested in virtual demolitions and small building by the end of 2021
Building materials are highly relevant in the context of circularity, due to their high volume of valuable material resources mixed in with the waste, as well as the potential recovery for the manufacturing of new building products. In particular, there is an increasing market for recycled aggregates and cementitious fractions derived from Construction and Demolition Waste (CDW). Wood can be recycled into oriented strand board (OSB), as well as mulch, compost, and other products. Metals -including steel, copper, and brass- are also valuable commodities to recycle.
Although this may suggest that the construction sector is highly circular, scrutiny of waste management practices reveals that CDW recovery is largely based on backfilling operations and low-grade recovery, such as using recycled aggregates in road sub-bases. Basic technology for the separation and recovery of CDW is well established, readily accessible and generally low cost. In general, 80% of CDW could, if properly managed, be recovered.
A key aspect of proper waste management is the advance selection and separation of materials: the better the separation of CDW, the more effective and the higher the quality of the recovered materials and products. Selective demolition emerges as the only valid solution in view of certain thresholds -material weights and volume and built surface- defined by public authorities. However, the feasibility of CDW recycling will greatly depend on the preliminary preparation of a realistic inventory of building elements and an accurate prediction of the resulting waste streams. It will boost better planning of the demolition works, as well as the optimization of on-site sorting activities, logistics, containers and transports, and final treatment.
National regulations in many countries specify the preparation of Waste Management Studies (WMS) for any construction or demolition project. Among other issues -the identification of hazardous materials and reusable elements-, this document must present the expected types and amounts of waste fractions. However, methods for waste quantification are not harmonized and the final decision relies on the demolition company or, more frequently, on the main contractor.
Building Information Modeling
Some WMS templates provided by professional associations of architects use the percentages based on the average composition of debris transported to CDW management plants. In some regions, tools, rates and recommendations are provided by the public bodies or environmental agencies. The slow but progressive digitalization of buildings and infrastructures –such as the use of Building Information Modeling (BIM)– gives additional opportunities to calculate waste with high accuracy in the new projects.
BIM methodology is increasingly global and has been adopted in construction projects across all stages of a building lifecycle. Nowadays, BIM models are mainly adopted within the design and construction phases, and to a lesser extent during the useful life of the buildings. The demolition stage in the context of BIM is a novel and growing area of research and development, the development of which is of great interest for companies. Reality capture techniques and related devices have been progressively tested in the scope of demolition activities. They have allowed a reduction of the time and effort required for generating a simple architectural model.
These techniques include the LIDAR laser scanning methods, which are evolving into portable and lighter devices as the Scanplan (FARO) or BLK2GO (LEIKA). Other alternatives to be considered are the Structure Sensor to be attached to a conventional iPad or the software solutions (MAGICPLAN) that take advantage of the technical capabilities of nowadays smartphones.
In ICEBERG project a new tool will be developed to support demolition planning and waste assessment, taking into account those recent solutions. Site visit for the initial survey will be complemented with a quick modeling and inventorying of the main elements through an agile process in a portable device (tablet). This will reduce the costs (<2€/m2 of built surface) and inventory time (two-thirds reduction compared to current versions) of these pre-demolition activities. This software (BIM4DW) will be developed in 2020 and 2021 and it will be based on Web3D standards. Its basic capabilities will be complemented with Application Programming Interfaces (APIs) to facilitate automatic filling of the model and a Demolition-Decision Making (DDM) module.
This tool will combine existing demolition/refurbishment planning systems (expert knowledge) and the information from the BIM4DW inventory, available resources, boundary conditions and criteria weighted by the user to find the most suitable demolition plan. The DDM will also include the circularity and environmental indicators of the selected demolition/refurbishment alternative. The solution will be tested in virtual demolitions and small building at the end of 2021, before being validated at several real scale demolition projects around Europe in 2022.
This software (BIM4DW) will be developed in 2020 and 2021 and will be based on Web3D standards
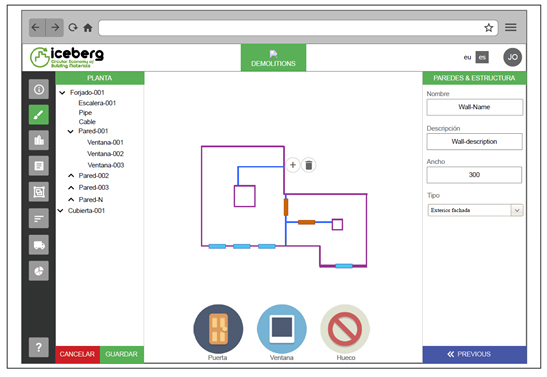