British Gypsum, ENVA and Loughborough University, partners on the ICEBERG project, are leading a project on advanced technologies for gypsum waste purification and processing
Miguel Castro-Díaz, Mohamed Osmani, Sergio Cavalaro, Paul Needham, Jeremy Thompson, Sam Elliott, Bill Parker, Tatiana Lovato and David Jalland 1.
Most gypsum (calcium sulphate dihydrate) waste from construction, refurbishment and demolition (CRD) ends up in landfill, where it may decompose, contributing to the generation of toxic hydrogen sulphide (H2S). The standard end-of-life plasterboard recycling process involves several steps aimed at removing impurities, namely manual segregation, grinding, sieving, and ferrous and non-ferrous magnetic separation.
However, one of the main challenges to obtaining suitable recycled gypsum from CRD plasterboard waste lies in the fact that it is difficult to obtain a consistent calcium sulphate dihydrate content of more than 92 wt% using current treatment technologies. In addition, plasterboard manufacturers face a reduction in the availability of desulphurisation gypsum (DSG), due to the closure of coal-fired power stations as a result of government efforts to tackle climate change, which means that DSG may be replaced by synthetic alternatives, such as phosphogypsum. Additionally, water-soluble impurities, such as chloride, magnesium, sodium and potassium salts, present in gypsum from CRD plasterboard and synthetic gypsum waste, , can impact the bonding properties of gypsum crystals.
The ICEBERG project assesses alternative purification treatments based on hydrocyclone separation and acid leaching, in terms of their potential to deliver calcium sulphate dihydrate contents and chemical purity values above 96 wt% in recycled gypsum from CRD plasterboard waste and phosphogypsum
Figure 1 shows non-segregated plasterboard waste from refurbishment and demolition collected at recycling sites in Nottingham and Leicester (UK) and used in this project. CRD plasterboard waste was crushed and sieved to obtain particle sizes of less than 250 microns to maximise the efficiency of the purification process.
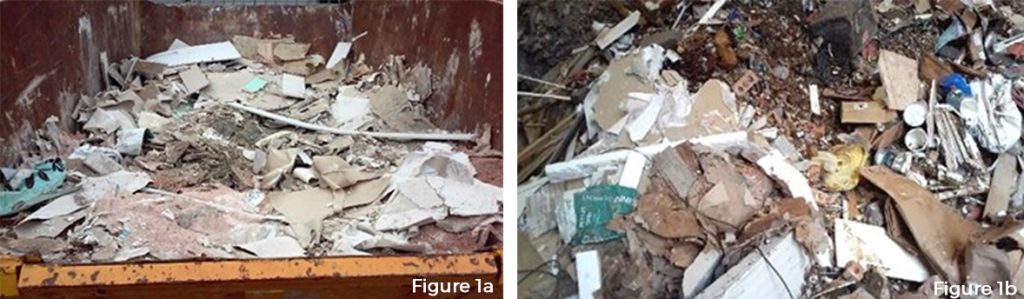
“Alternative purification treatments based on hydrocyclone separation and acid leaching have been assessed”
A 2-inch Salter hydrocyclone was assembled with a centrifugal pump and mixing tank for hydrocyclone separation testing. Hydrocyclone tests lasted 3 hours, with samples being collected from the bottom of the hydrocyclone every hour. Acid leaching tests were performed using a borosilicate beaker, a hotplate and an overhead stirrer placed inside a fume cupboard. Acid leaching tests were conducted using a gypsum/solution ratio of 1:3 wt/wt, slurry volume of 350 mL, stirring speed of 150 revolutions per minute, temperatures of 24°C, 60°C and 90°C, residence times of 30 minutes, 1 hour, 1.5 hours, 2 hours and 3 hours, and sulphuric acid concentrations of 3 wt%, 5 wt% and 10 wt%. Collected samples from hydrocyclone separation and acid leaching tests were filtrated and dried at 45°C.
Hydrocyclone separation for up to 3 hours did not have a significant impact on the chemical composition of gypsum from CRD plasterboard waste and phosphogypsum. Furthermore, foam formed during the hydrocyclone separation process (Figure 2).
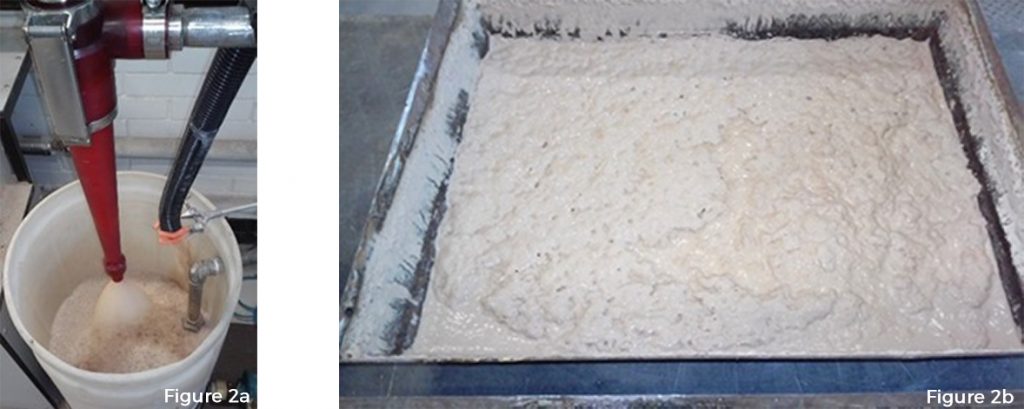
On the other hand, leaching with sulphuric acid (H2SO4) at 90°C for either 30 minutes (phosphogypsum) or 1 hour (CRD waste gypsum) using a 5 wt% H2SO4 aqueous solution gave chemical purity values and calcium sulphate dihydrate contents above the target 96 wt% in all samples. Figure 3 shows the chemical purity values obtained after acid leaching of phosphogypsum. Gypsum chemical purity is defined here as the sum of CaSO4 and other oxides that are inherent minor constituents of natural gypsum (SiO2, Al2O3, Fe2O3, Ni2O3 and SrO) and do not have any detrimental effect on gypsum properties.
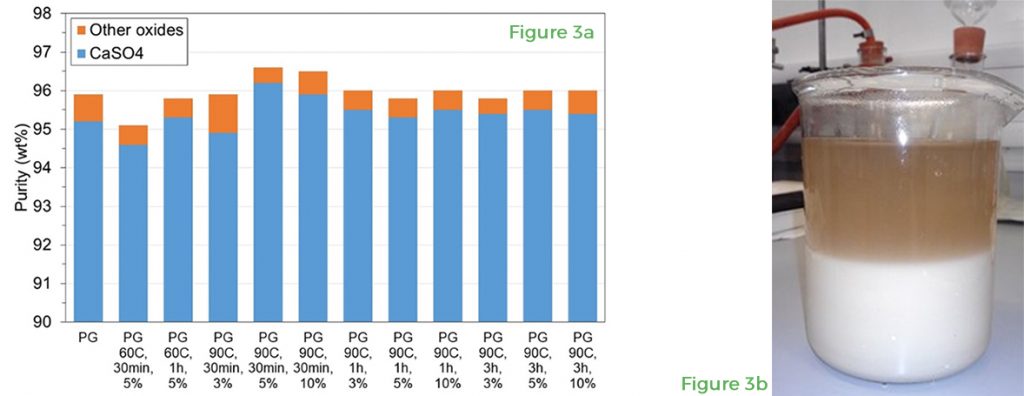
In terms of calcium sulphate dihydrate content, leaching with H2SO4 increased the calcium sulphate dihydrate content in the recycled material, in part because H2SO4 reacts with calcium carbonate (CaCO3) in gypsum from CRD plasterboard waste and phosphogypsum to produce more calcium sulphate dihydrate and carbon dioxide. The calcium sulphate hemihydrate phase present in gypsum from CRD plasterboard waste and phosphogypsum was converted into calcium sulphate dihydrate after acid leaching.
Ongoing work is focusing on the rheological characterisation and determination of the setting times of recycled gypsum plasters compared to business-as-usual gypsum plaster to validate the acid leaching purification process for circular plasterboard manufacturing, and on the valorisation of the acidic wastewater produced in the process.
1 Authors:Miguel Castro-Díaz, Mohamed Osmani and Sergio Cavalaro (School of Architecture, Building and Civil Engineering, Loughborough University, UK); Paul Needham, Jeremy Thompson and Sam Elliott (ENVA, UK); Bill Parker, Tatiana Lovato and David Jalland (British Gypsum, UK)